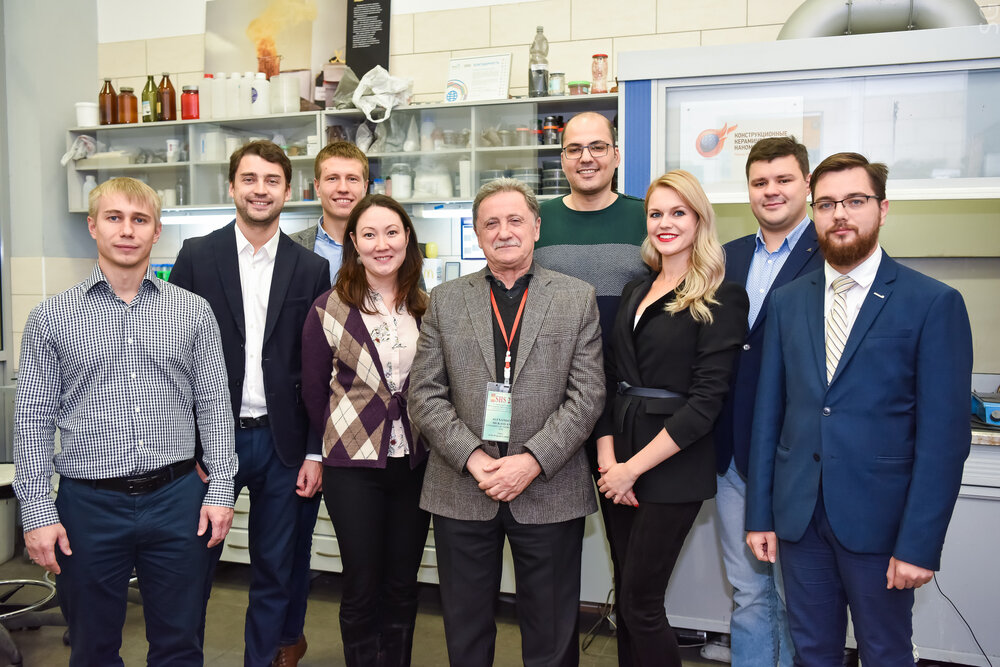
Um grupo de cientistas da NUST MISIS desenvolveu um material cerâmico com o maior ponto de fusão entre os compostos atualmente conhecidos. Devido à combinação única de propriedades físicas, mecânicas e térmicas, o material é promissor para uso nos componentes mais carregados de calor das aeronaves, como carenagens no nariz, motores a jato e bordas frontais afiadas das asas, operando a temperaturas acima de 2000 graus C. Os resultados são publicados na Ceramics International.
Muitas agências espaciais líderes (NASA, ESA, bem como agências do Japão, China e Índia) estão desenvolvendo ativamente aviões espaciais reutilizáveis, o que reduzirá significativamente o custo de entrega de pessoas e cargas em órbita, além de reduzir os intervalos de tempo entre os vôos.
“Atualmente, resultados significativos foram alcançados no desenvolvimento de tais dispositivos. Por exemplo, reduzir o raio de arredondamento das arestas frontais das asas para alguns centímetros leva a um aumento significativo na sustentação e manobrabilidade, além de reduzir o arrasto aerodinâmico No entanto, ao sair da atmosfera e entrar novamente nela, na superfície das asas do avião espacial, podem ser observadas temperaturas de cerca de 2000 graus C, chegando a 4000 graus C na extremidade, portanto, quando se trata de tais aeronaves, há uma pergunta associada à criação e desenvolvimento de novos materiais que podem funcionar em temperaturas tão altas “, diz Dmitry Moskovskikh, chefe do NUST MISIS Center for Constructional Ceramic Materials.
Durante desenvolvimentos recentes, o objetivo dos cientistas era criar um material com o mais alto ponto de fusão e altas propriedades mecânicas. O sistema triplo de háfnio-carbono-nitrogênio, carbonitreto de háfnio (Hf-CN), foi escolhido, como cientistas da Brown University (EUA) previram anteriormente que o carbonitreto de háfnio teria uma alta condutividade térmica e resistência à oxidação, além da maior fusão ponto entre todos os compostos conhecidos (aproximadamente 4200 graus C).
Usando o método de síntese autopropagável a alta temperatura, os cientistas da NUSTMISIS obtiveram HfC0.5N0.35 (carbonitreto de háfnio) próximo à composição teórica, com uma alta dureza de 21,3 GPa, que é ainda maior do que em novos materiais promissores, como ZrB2 / SiC (20,9 GPa) e HfB2 / SiC / TaSi2 (18,1 GPa).
“É difícil medir o ponto de fusão de um material superior a 4000 graus C. Portanto, decidimos comparar as temperaturas de fusão do composto sintetizado e o campeão original, o carboneto de háfnio. Para isso, colocamos amostras de HFC e HfCN compactadas em um placa de grafite em forma de haltere, e cobriu a parte superior com uma placa semelhante para evitar a perda de calor “, diz Veronika Buinevich, estudante de pós-graduação da NUST MISIS.
Em seguida, eles a conectaram a uma bateria usando eletrodos de molibdênio. Todos os testes foram realizados em vácuo profundo. Como a seção transversal das placas de grafite difere, a temperatura máxima foi atingida na parte mais estreita. Os resultados do aquecimento simultâneo do novo material, carbonitreto e carbeto de háfnio, mostraram que o carbonitreto tem um ponto de fusão mais alto que o carbeto de háfnio.
No entanto, no momento, o ponto de fusão específico do novo material está acima de 4000 graus C e não pôde ser determinado com precisão em laboratório. No futuro, a equipe planeja realizar experimentos para medir a temperatura de fusão por pirrometria de alta temperatura usando um laser ou resistência elétrica. Eles também planejam estudar o desempenho do carbonitreto de háfnio resultante em condições hipersônicas, o que será relevante para futuras aplicações na indústria aeroespacial.
Publicado em 30/05/2020 20h39
Artigo original:
Estudo original:
Achou importante? Compartilhe!
Assine nossa newsletter e fique informado sobre Astrofísica, Biofísica, Geofísica e outras áreas. Preencha seu e-mail no espaço abaixo e clique em “OK”: