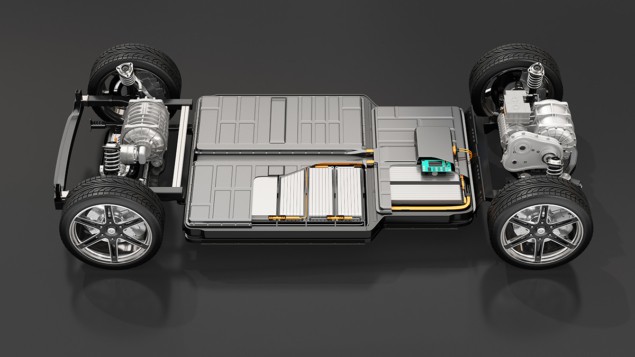
Projetar componentes estruturais que podem alimentar um veículo elétrico requer um regime de testes abrangente para avaliar a resistência, rigidez e estabilidade térmica dos materiais da bateria
Os avanços contínuos na tecnologia de baterias tornaram pela primeira vez os veículos elétricos uma alternativa viável aos carros movidos a combustíveis fósseis. No entanto, mais inovação será crucial para impulsionar a adoção generalizada de veículos movidos a bateria ? em particular para projetar dispositivos aprimorados de armazenamento de energia para permitir que os motoristas viajem mais com uma única carga ? e para que as soluções elétricas sejam estendidas a outros modos de transporte, como a aviação.
Uma abordagem explorada por Jodie Lutkenhaus e sua equipe na Texas A&M University é projetar baterias e supercapacitores que também possam se tornar parte da estrutura de suporte de carga do veículo. Esses dispositivos estruturais de armazenamento de energia podem fornecer mais energia sem adicionar peso extra, melhorando a eficiência de combustível de veículos elétricos e potencialmente oferecendo uma fonte secundária de energia para aeronaves. “Em um avião comercial, por exemplo, baterias embutidas no piso podem fornecer energia para as telas sensíveis ao toque e outros equipamentos elétricos na cabine”, explica Lutkenhaus. “No geral, isso pode melhorar a eficiência do combustível porque você não está usando tanta energia para alimentar os componentes elétricos.”
Os materiais multifuncionais que estão sendo desenvolvidos para esses dispositivos estruturais devem oferecer uma combinação desafiadora de propriedades. A maioria dos materiais de eletrodos são pulverulentos, com porosidade suficiente para permitir o transporte eficiente de íons, enquanto os componentes estruturais precisam ser rígidos e fortes. “Estamos tentando criar baterias e capacitores que imitam as propriedades de compósitos estruturais feitos de epóxi reforçado com fibra de carbono”, explica Lutkenhaus. “Usamos aditivos como grafeno e nanofibras de Kevlar para melhorar a rigidez, mas eles não são muito ativos. Eles diluem o comportamento de bateria em favor das propriedades mecânicas.”
Lutkenhaus e sua equipe abordaram o problema por meio da química interfacial, aprimorando a ligação entre o aditivo e o material do eletrodo para reduzir a quantidade de aditivo necessária para fortalecer o material. Em um estudo de pesquisa recente, eles demonstraram que supercapacitores feitos de óxido de grafeno reduzido (rGO) podem ser fortalecidos modificando quimicamente a estrutura usando polidopamina, um polímero altamente adesivo, e adicionando apenas uma pequena quantidade de nanofibras de Kevlar. “Você pode apenas polvilhar um pouco das nanofibras e as propriedades mecânicas aumentam”, diz Lutkenhaus.
A avaliação das propriedades desses materiais multifuncionais requer um conjunto abrangente de testes. Para sondar as propriedades mecânicas dos eletrodos, Lutkenhaus e sua equipe exploram um analisador mecânico dinâmico (DMA) da TA Instruments, que é mais comumente usado para medir as mudanças nas propriedades mecânicas à medida que a temperatura varia ou quando o estresse ou a tensão são aplicados. “Estamos usando-o mais como um testador de tração, o que é um pouco incomum”, comenta Lutkenhaus. “Usamos o DMA porque os eletrodos da bateria são muito finos, em torno de 100 mícrons. O DMA fornece um arranjo de filme fino e braçadeira de fibra que nos permite medir propriedades como módulo, tenacidade e tensão final.”
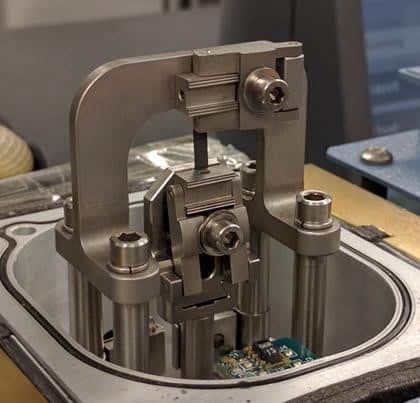
Lutkenhaus e sua equipe também usaram nanofibras de Kevlar para projetar separadores de bateria, que fornecem uma barreira física entre o ânodo e o cátodo para evitar curtos-circuitos, mas ainda precisam permitir que os íons se movam entre os dois. “Os separadores de bateria são realmente difíceis de projetar”, diz Lutkenhaus. “Eles precisam de uma combinação desafiadora de propriedades, incluindo boa condutividade iônica, robustez mecânica e estabilidade térmica em uma ampla faixa de temperatura.”
Lutkenhaus ressalta que o separador comercial mais comum usado em baterias de íons de lítio, chamado Celgard, começa a se degradar em temperaturas mais altas. “O material passa por uma transição de derretimento ou amolecimento que eventualmente faz com que a bateria falhe”, explica ela. “Em nosso estudo, precisávamos identificar quaisquer transições térmicas que limitassem a temperatura de operação da bateria”
Lutkenhaus e sua equipe compararam as propriedades térmicas do separador Celgard padrão com um baseado em nanofibras de Kevlar. Para medir o comportamento térmico, eles usaram um calorímetro de varredura diferencial (DSC) da TA Instruments, que em diferentes temperaturas mede a quantidade de calor necessária para alterar a temperatura do material. Como esperado, os perfis de DSC revelaram que o Celgard começou a derreter em torno de 160°C, e no resfriamento recristalizou a 113°C. Em contraste, o separador à base de Kevlar não mostra nenhuma mudança no comportamento térmico em temperaturas de até 400 °C. “É o caso único em que você está fazendo experimentos na esperança de obter uma linha plana, porque você não quer ver nenhuma assinatura térmica”, diz Lutkenhaus.
Outros testes investigaram a temperatura na qual a estrutura física dos separadores começa a quebrar. Usando um analisador termogravimétrico (TGA) da TA Instruments, que mede a massa da amostra à medida que a temperatura aumenta, os pesquisadores descobriram que o Celgard começa a perder massa em torno de 270 ° C, enquanto o separador baseado em Kevlar pode ser aquecido a quase 450 °C antes de apresentar qualquer sinal de degradação. As nanofibras à base de Kevlar também se auto-extinguem quando expostas a uma chama ? um importante recurso de segurança para baterias ? enquanto as versões comerciais do Celgard encolhem em condições secas e queimam completamente quando molhadas com um eletrólito.
Testes mecânicos com um DMA mostram que, em condições secas, o separador baseado em Kevlar tem um módulo de Young cerca de 1.000 vezes maior do que a versão comercial da Celgard, e resistência e rigidez amplamente equivalentes quando molhado. Enquanto isso, medições de fluência que sondam o comportamento mecânico do material sob uma tensão constante revelam que o separador Celgard se estende em temperaturas mais altas, consistente com o efeito de fusão e amolecimento observado em seu perfil térmico. “O separador à base de Kevlar não apresenta nenhuma deformação em temperaturas de até 400 °C, novamente apresentando melhor estabilidade térmica do que os separadores disponíveis comercialmente”, comenta Lutkenhaus.
Lutkenhaus acredita que as propriedades térmicas superiores dos separadores baseados em nanofibras de Kevlar os tornariam adequados para dispositivos de armazenamento de energia operando em ambientes extremos. No entanto, é necessário mais trabalho para aumentar suas propriedades eletroquímicas, uma vez que a integração do separador baseado em Kevlar em uma bateria de íons de lítio resultou em uma capacidade ligeiramente reduzida em comparação com a versão Celgard, bem como uma queda significativa na capacidade após 50 ciclos de carga/descarga .
Lutkenhaus e sua equipe também estão investigando o potencial da fibra de carbono, comumente usada em compósitos estruturais, para atuar como matriz mecânica para materiais de bateria. A incorporação de materiais de eletrodos em fibra de carbono demonstrou produzir dispositivos rígidos e fortes, mas ainda não armazenam energia suficiente para rivalizar com as baterias de íons de lítio padrão. “Também temos muito interesse no comportamento térmico porque os veículos que precisam de baterias estruturais podem operar em temperaturas mais baixas ou em um deserto de alta temperatura”, diz Lutkenhaus. “Além disso, precisamos começar a pensar nos efeitos do impacto mecânico nesses dispositivos para entender como eles podem se comportar em um acidente.”
Publicado em 06/02/2022 19h39
Artigo original: